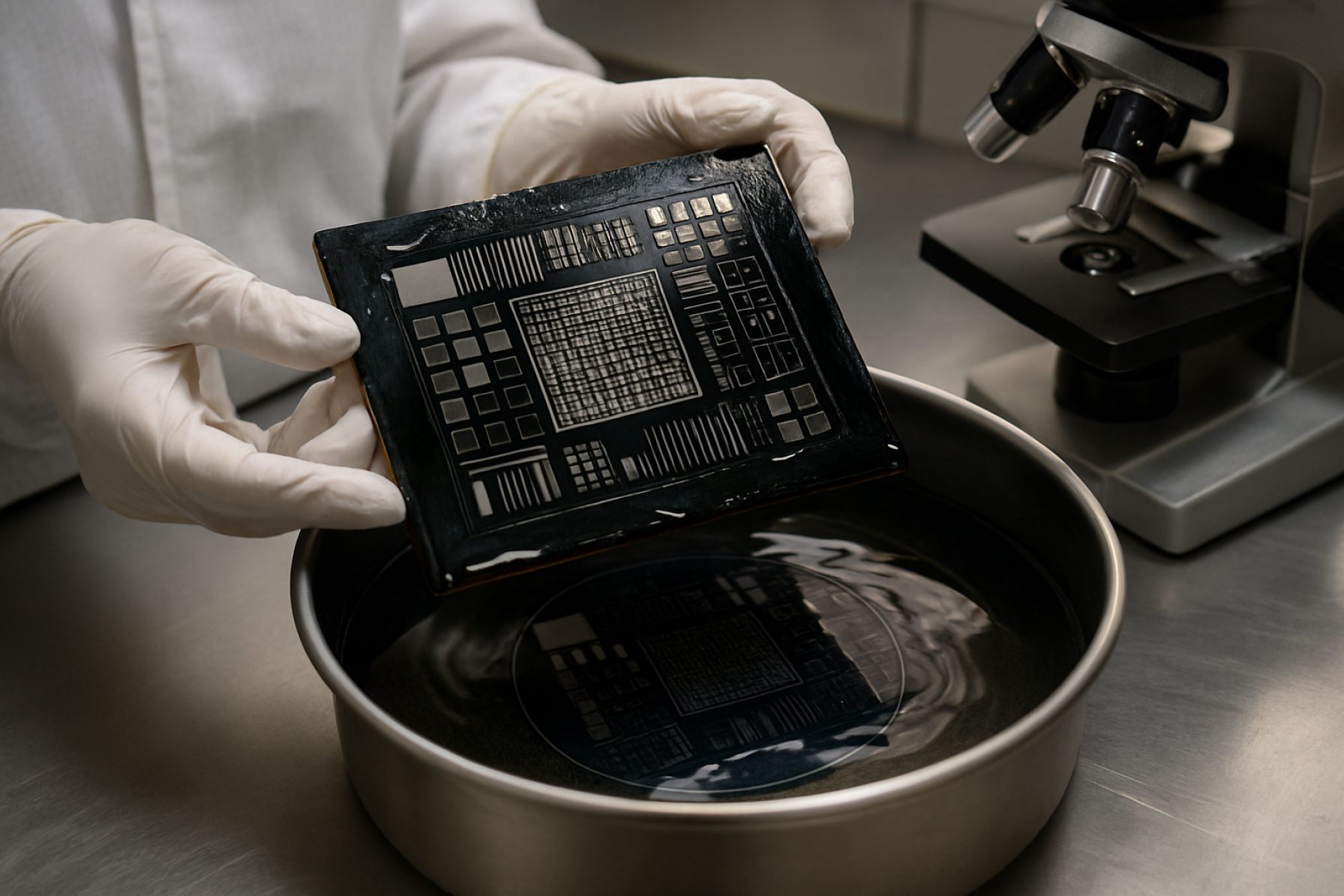
Wet Plate Photolithography 2025–2029: Unveiling Game-Changing Breakthroughs in Microfabrication
Table of Contents
- Executive Summary: Key Trends and Market Drivers
- Technology Overview: Fundamentals of Wet Plate Photolithography
- Latest Innovations: 2025’s Cutting-Edge Processes and Materials
- Major Industry Players and Official Partnerships
- Market Forecast 2025–2029: Growth Sectors and Revenue Projections
- Comparative Analysis: Wet Plate vs. Dry and Alternative Lithography Methods
- Emerging Applications: Electronics, MEMS, and Photonics
- Sustainability and Environmental Impact—Official Standards and Initiatives
- Challenges and Barriers: Technical, Economic, and Regulatory Outlook
- Future Roadmap: Next-Gen Opportunities and Strategic Recommendations
- Sources & References
Executive Summary: Key Trends and Market Drivers
Wet plate photolithography, a cornerstone technology in semiconductor and microfabrication industries, continues to evolve rapidly as manufacturers pursue higher throughput, finer patterning, and improved process control. In 2025, the sector is experiencing renewed momentum driven by escalating demand for advanced packaging, heterogeneous integration, and next-generation nodes in both logic and memory applications.
Key trends shaping the market include the integration of wet plate photolithography into advanced semiconductor manufacturing lines and the transition toward high-resolution, low-defect processes. Companies are investing in the automation and digitization of wet processing equipment to address the stringent requirements of sub-10 nm and advanced 3D architectures. Leading equipment suppliers such as Tokyo Ohka Kogyo Co., Ltd. and SCREEN Semiconductor Solutions are at the forefront, offering highly configurable wet stations with advanced chemical management and real-time process monitoring. These innovations help reduce process variability and enhance yield, responding to the semiconductor industry’s demand for zero-defect manufacturing.
Environmental sustainability and chemical cost optimization are additional market drivers. The push for greener fabs is leading to increased adoption of closed-loop recirculation and reclamation systems within wet benches, as well as tighter controls on chemical usage and effluent treatment. Equipment makers like Lam Research are developing solutions that minimize footprint and resource consumption while maintaining the precision required for leading-edge devices.
Geopolitical factors and supply chain localization efforts, particularly in the US, EU, and East Asia, are prompting both established and emerging fabs to invest in new wet photolithography lines. This expansion is bolstered by government incentives for domestic chip production and ongoing capital expenditures from major foundries and IDMs. For instance, TSMC and Samsung Electronics are ramping up capacity with state-of-the-art wet process technologies to support advanced logic and memory products.
Looking ahead, the market outlook remains robust through the late 2020s, fueled by the proliferation of AI, 5G, and automotive electronics. Wet plate photolithography will remain a critical enabler, with ongoing R&D focused on defect reduction, process integration, and compatibility with novel photoresists and substrates. The industry’s trajectory is firmly aligned with the demands for higher density, greater efficiency, and sustainability in semiconductor manufacturing.
Technology Overview: Fundamentals of Wet Plate Photolithography
Wet plate photolithography remains a cornerstone technique within semiconductor and microfabrication industries, particularly for processes where high throughput and cost-effective patterning are prioritized. The fundamental principle involves applying a liquid photoresist to a substrate, commonly via spin coating, to form a uniform, photosensitive layer. Subsequent exposure to patterned ultraviolet (UV) light through a photomask initiates chemical changes in the resist, enabling selective development and etching to transfer intricate patterns onto the substrate.
Current advances in 2025 see ongoing refinement of wet plate photolithography methods. For example, improvements in spin coating technology—such as enhanced resist uniformity and reduced edge bead formation—have been implemented by leading equipment providers like SÜSS MicroTec and EV Group. These advancements support tighter critical dimension (CD) control, crucial for advanced packaging and MEMS (micro-electro-mechanical systems) fabrication.
In addition, novel resist chemistries are being introduced to address the demand for higher resolution and sensitivity at lower exposure doses. Companies such as JSR Micro and TOKYO OHKA KOGYO CO., LTD. have released new formulations specifically optimized for deep ultraviolet (DUV) and i-line lithography, enabling finer patterning capabilities while maintaining compatibility with wet processing environments.
A notable trend in 2025 is the integration of wet plate photolithography with advanced alignment and automation systems. For instance, Canon Inc. and Nikon Corporation continue to refine aligner technologies, offering sub-micron alignment accuracy and in-situ process monitoring. This enables higher yields and reduces manual intervention, aligning with the industry’s push towards smarter, more automated fabs.
Looking ahead to the next few years, industry outlook suggests that wet plate photolithography will remain vital for applications such as MEMS, sensors, compound semiconductors, and advanced packaging, where ultra-fine node sizes are not always required. Continuous improvements in resist materials, coater-developer systems, and mask alignment are expected to further bolster the reliability and performance of wet processing. Industry collaborations, such as those fostered by SEMI’s global standards initiatives, will also drive interoperability and process optimization across equipment and materials suppliers (SEMI).
Latest Innovations: 2025’s Cutting-Edge Processes and Materials
Wet plate photolithography, a cornerstone in microfabrication, continues to evolve rapidly as the semiconductor industry faces relentless pressure for higher throughput, precision, and cost-effectiveness. In 2025, innovations are centered around process automation, novel photoresist chemistries, and eco-friendly developer solutions, each addressing critical bottlenecks in device scaling and sustainable manufacturing.
A prominent trend this year is the integration of advanced robotics and closed-loop metrology within wet processing tracks. Leading system suppliers such as Tokyo Ohka Kogyo and SÜSS MicroTec have announced new generations of wet bench and cluster tools featuring real-time defect inspection and adaptive process control. These systems employ AI-driven analytics for in-situ monitoring of photoresist coating uniformity, development rates, and critical dimension (CD) control, directly addressing yield challenges at advanced nodes.
Material science breakthroughs are also shaping the wet plate photolithography landscape. The ongoing transition to metal oxide and hybrid organic-inorganic resists, spearheaded by companies like JSR Micro, has led to photoresists with superior etch resistance, higher resolution, and lower line edge roughness. In 2025, JSR Micro’s latest chemically amplified resists are being tailored for both i-line and deep UV (DUV) lithography, supporting sub-50 nm process geometries and facilitating simpler pattern transfer for advanced packaging and MEMS applications.
Sustainability is another focal point. Major manufacturers are commercializing developer and rinse chemicals with reduced toxicity and improved recyclability. BASF has introduced new aqueous-based developer formulations that significantly minimize waste and lower energy consumption during post-exposure bake and development stages. These solutions are being adopted by fabs aiming to comply with stricter environmental regulations and to reduce operational costs.
Looking ahead to the next few years, the outlook is for further convergence of wet plate photolithography with wafer-level packaging and 3D integration technologies. Industry bodies such as SEMI are actively coordinating roadmap workshops to standardize wet process compatibility with advanced substrates and to enable higher overlay accuracy across heterogeneous integration schemes.
In summary, the 2025 landscape for wet plate photolithography is defined by smarter equipment, innovative resist chemistries, and greener process chemicals—collectively enabling finer patterning, higher yields, and more sustainable semiconductor manufacturing.
Major Industry Players and Official Partnerships
As of 2025, the wet plate photolithography landscape remains shaped by a concentrated group of major industry players, each leveraging advanced R&D and strategic alliances to push the boundaries of semiconductor and microfabrication processes. Leading equipment manufacturers such as ASML Holding NV and Canon Inc. continue to supply photolithography tools—including those that support wet processing modules—enabling high-throughput and fine-resolution patterning for integrated circuit (IC) production. These companies are integrating wet plate processes with advanced lithographic techniques to address challenges in critical dimension control and defect reduction.
On the materials and chemical consumables front, TOK (Tokyo Ohka Kogyo Co., Ltd.) and FUJIFILM Corporation are global suppliers of photoresists and ancillary chemicals tailored for wet plate applications. These firms have formed official partnerships with semiconductor fabs and equipment makers to ensure their products meet next-generation device scaling needs, especially as nodes approach sub-10 nm regimes.
Collaborative efforts are also seen between equipment suppliers and foundry operators. For instance, TSMC has maintained close technical relationships with both ASML Holding NV and TOK, jointly developing wet photolithography processes that optimize yield and performance for advanced logic and memory devices. Such partnerships are often formalized through joint development agreements or material qualification programs, ensuring seamless integration of wet plate photolithography into high-volume manufacturing lines.
In addition, semiconductor equipment suppliers such as Lam Research Corporation provide integrated wet processing platforms that complement lithography tools, further solidifying the interconnectedness of the supply chain. These collaborations are essential for developing next-generation wet processing solutions that can handle the rigorous demands of increasingly complex device architectures.
Looking ahead, the outlook for wet plate photolithography is marked by increased investment in automation, defect control, and eco-friendly chemical processes. Industry players are expected to deepen official partnerships, particularly as the sector addresses EUV integration and 3D device fabrication challenges. The coming years will likely see more consortiums and joint innovation programs, as the ecosystem rallies to deliver the precision and scalability required for future semiconductor advancements.
Market Forecast 2025–2029: Growth Sectors and Revenue Projections
Wet plate photolithography remains a foundational process in semiconductor and microfabrication industries, but its market dynamics are shifting rapidly in the years 2025–2029. The sector is expected to see moderate growth, primarily driven by the demand for mature node semiconductors (65 nm and above), MEMS, compound semiconductors, and specialty devices where cost-effective, high-throughput processes are critical. Despite the rise of advanced lithography technologies for cutting-edge nodes, wet plate photolithography continues to serve essential roles in legacy process lines, sensor manufacturing, and emerging applications such as microfluidics and photonic devices.
- Growth Sectors: The most significant revenue drivers for wet plate photolithography equipment and consumables will come from mature logic and analog IC fabrication, power devices, and automotive electronics. The global adoption of electric vehicles (EVs) and the expansion of 5G/6G infrastructure necessitate large volumes of MEMS sensors and RF components, much of which relies on established wet photolithography processes. Additionally, the proliferation of IoT devices and increased investment in digital healthcare (e.g., lab-on-chip and biosensors) are expected to boost demand for wet plate lines, especially in Asia-Pacific manufacturing hubs (Tokyo Ohka Kogyo Co., Ltd., Sumitomo Chemical).
- Revenue Projections: Leading wet process equipment suppliers and photoresist manufacturers are forecasting steady, if modest, year-on-year growth. For example, Tokyo Ohka Kogyo Co., Ltd. and JSR Corporation have indicated ongoing investments to support mature process nodes and specialty applications. Market analysts within these firms anticipate CAGR in the range of 3–5% for wet plate photolithography-related products through 2029, with total market size projected to exceed several billion USD by the end of the forecast period, largely driven by recurring consumables sales and periodic line upgrades within foundries and IDMs (ULVAC, Inc.).
- Regional Outlook: The Asia-Pacific region, particularly Taiwan, China, South Korea, and Japan, will continue to dominate both capacity expansion and consumption of wet plate photolithography equipment and materials. Companies such as ULVAC, Inc. and Tokyo Ohka Kogyo Co., Ltd. are expanding production and support services to address this sustained demand. Meanwhile, North America and Europe will see investments primarily in specialty and R&D fabrication lines.
Looking ahead, while the market for advanced dry and EUV lithography will outpace wet photolithography in terms of innovation, the latter’s entrenched role in high-volume, cost-sensitive manufacturing ensures a stable outlook for the technique and its supply chain through 2029.
Comparative Analysis: Wet Plate vs. Dry and Alternative Lithography Methods
In 2025, wet plate photolithography remains a cornerstone of semiconductor fabrication, but the landscape is shifting rapidly as dry and alternative lithography methods mature. Wet plate techniques, which involve the application of a liquid photoresist onto substrates followed by exposure and development, have traditionally offered high throughput and cost efficiency for feature sizes above 28 nm. Companies such as Tokyo Ohka Kogyo Co., Ltd. and JSR Corporation continue to supply advanced photoresists and process materials, supporting incremental improvements in resolution and defect control.
However, as the industry pushes toward sub-10 nm nodes, the limitations of wet plate photolithography become increasingly apparent. Critical challenges include resist profile control, line edge roughness, and defectivity, especially for advanced logic and memory applications. Dry lithography methods, such as dry etching and plasma-enhanced processes, offer superior pattern fidelity and are less susceptible to issues such as resist collapse that can occur with wet processes. Leading equipment providers like Lam Research have advanced dry etch technologies that complement or even replace some wet process steps in cutting-edge nodes.
Alternative lithography techniques, most notably Extreme Ultraviolet (EUV) lithography, have entered high-volume production in 2025. ASML is at the forefront, supplying EUV scanners capable of resolving sub-7 nm features with far fewer process steps compared to multi-patterning wet photolithography. EUV’s adoption is accelerating, particularly for leading-edge foundries, due to its ability to reduce complexity and improve yield. Nevertheless, the high capital and operational costs of EUV, as well as infrastructure challenges, mean wet plate methods remain prevalent for mature nodes and specialty devices where cost pressures dominate.
Looking ahead over the next few years, hybrid approaches are gaining traction. Semiconductor manufacturers are increasingly combining wet and dry techniques, leveraging the strengths of each to optimize cost, throughput, and device performance. For instance, patterning strategies often use wet plate photolithography for less critical layers and turn to dry or EUV methods for the most demanding levels. Industry consortia such as SEMI continue to coordinate research on next-generation lithography, including improvements in wet process chemistry and defect mitigation.
In summary, while wet plate photolithography will remain indispensable for many applications through the latter half of the 2020s, its comparative advantages are narrowing as dry and alternative methods advance. The ongoing evolution points toward a diversified lithography ecosystem, where process selection is increasingly dictated by device requirements, cost, and sustainability considerations.
Emerging Applications: Electronics, MEMS, and Photonics
Wet plate photolithography, a cornerstone in microfabrication, is experiencing renewed interest for emerging applications in electronics, MEMS (Micro-Electro-Mechanical Systems), and photonics as of 2025. This technique, which employs liquid photoresists spun or coated onto substrates followed by UV exposure and chemical development, continues to evolve alongside demands for higher resolution, finer pattern fidelity, and process flexibility.
In the electronics sector, wet plate photolithography remains integral to advanced IC (Integrated Circuit) and PCB (Printed Circuit Board) manufacturing. Recent advancements focus on optimizing photoresist formulations and coating technologies to support sub-1 μm features. Companies like TOKYO OHKA KOGYO CO., LTD. and MicroChem Corp. are investing in new resist chemistries and anti-reflective coatings to enhance critical dimension control and defect reduction. Furthermore, equipment manufacturers such as SÜSS MicroTec have introduced high-throughput spin coaters and mask aligners designed for volume production, addressing the semiconductor industry’s shift towards heterogeneous integration and advanced packaging.
Within MEMS fabrication, wet plate photolithography is valued for its versatility and scalability, enabling the production of pressure sensors, accelerometers, and microfluidic devices. The increasing integration of MEMS into automotive and healthcare electronics is driving process improvements. For example, STMicroelectronics utilizes advanced photolithography modules to fabricate MEMS sensors at wafer-level, leveraging multi-layer resist stacks for complex 3D microstructures. Process enhancements reported by ULVAC, Inc. include optimized wet development and resist stripping systems, contributing to higher MEMS device yields and reliability.
Photonics applications—such as integrated photonic circuits, waveguides, and diffractive optics—are also benefiting from innovations in wet plate photolithography. Precise patterning of optical elements on glass and silicon substrates is enabled by photoresists developed by Dow and Kayaku Advanced Materials, Inc., supporting device miniaturization and wavelength-specific performance. The rise of silicon photonics for datacom and sensing is prompting foundries like LioniX International to implement high-resolution lithography flows, enabling rapid prototyping and pilot-scale manufacturing.
Looking ahead, wet plate photolithography is expected to maintain relevance by integrating with complementary techniques (such as nanoimprint and dry etching) and by supporting new materials and hybrid processes. Industry stakeholders anticipate further automation and digitalization of lithography lines, with a focus on yield improvement and process sustainability through reduced chemical usage and recycling initiatives.
Sustainability and Environmental Impact—Official Standards and Initiatives
As semiconductor manufacturing continues to advance, the industry’s focus on sustainability and environmental impact has intensified, especially regarding wet plate photolithography techniques. In 2025 and the coming years, official standards and sector-wide initiatives are shaping cleaner and safer photolithography processes, with major stakeholders striving to reduce chemical waste, energy consumption, and environmental footprint.
A key development is the revision and enforcement of international standards through bodies such as the SEMI (Semiconductor Equipment and Materials International), whose guidelines like SEMI S2 (Environmental, Health, and Safety Guideline for Semiconductor Manufacturing Equipment) and SEMI S8 (Ergonomics Engineering) are increasingly referenced for photolithography tools. These standards address safe chemical handling, exhaust management, and the minimization of hazardous emissions, directly influencing the design and operation of track systems and wet benches used in wet plate processes.
Leading equipment manufacturers are also aligning with these standards and adopting green initiatives. For example, Tokyo Ohka Kogyo Co., Ltd. (TOK) and JSR Corporation—two major suppliers of photoresists and specialty chemicals—have launched sustainability programs focusing on waste reduction, water purification, and the development of less toxic photoresist formulations. TOK’s “Sustainable Manufacturing” initiative includes investments in closed-loop water systems and advanced waste treatment at its photolithography chemical plants, while JSR’s “Eco-Friendly Materials” campaign aims to launch new resist products with reduced volatile organic compound (VOC) content by 2026.
Another significant shift comes from semiconductor fabs’ engagement with global environmental stewardship programs. TSMC, the world’s largest contract chipmaker, has set targets for lowering greenhouse gas emissions and water usage per wafer, including in wet lithography stages. Their 2025 environmental roadmap involves recycling upwards of 85% of process water and implementing energy recovery systems in photolithography cleanrooms, reflecting a broader trend among leading fabs.
Meanwhile, the Semiconductor Industry Association (SIA) is promoting cross-company collaboration to standardize environmental metrics and reporting specific to wet chemical processes, including photolithography. These efforts are expected to result in new best-practice guidelines by 2026, aimed at harmonizing global environmental compliance and driving continuous improvements in sustainability.
Looking forward, the sector anticipates further tightening of regulations on hazardous substances and process emissions, alongside greater adoption of circular economy models for photolithography materials. As corporate accountability and regulatory scrutiny grow, wet plate photolithography is likely to see accelerated innovation in greener chemistries and process integration, supporting the dual goals of technological progress and environmental stewardship.
Challenges and Barriers: Technical, Economic, and Regulatory Outlook
Wet plate photolithography continues to play a critical role in semiconductor and microfabrication industries, yet it faces several key challenges and barriers as of 2025. From technical limitations to economic and regulatory pressures, the outlook for this technique is shaped by both longstanding issues and emerging trends.
- Technical Challenges: Wet plate photolithography is inherently constrained by resolution limits, substrate compatibility, and uniformity issues. As device geometries shrink, conventional wet processes struggle to achieve the sub-20 nm resolution required for cutting-edge integrated circuits. Defect control, resist adhesion, and pattern collapse are persistent issues, particularly for advanced nodes. Equipment providers such as Lam Research Corporation and SCREEN Holdings Co., Ltd. are actively developing new wet processing tools and chemistries, but improvements often come with increased complexity and cost.
- Economic Barriers: The cost-effectiveness of wet plate techniques is challenged by the demand for higher throughput and tighter process control. As leading foundries like Taiwan Semiconductor Manufacturing Company (TSMC) and Intel Corporation push toward more advanced nodes, investments in alternative lithography (such as EUV) tend to outpace upgrades in wet processes. Additionally, the use of high-purity chemicals and water, as well as the management of waste streams, increases operational costs for fabrication facilities. Economic pressures may limit the adoption of wet plate photolithography for next-generation devices, reserving it mainly for mature process nodes and specialty applications.
- Regulatory and Environmental Outlook: Stricter environmental regulations on chemical usage and wastewater discharge are becoming more prominent, especially in regions with aggressive sustainability targets. Regulatory bodies and industry organizations—such as Semiconductor Industry Association (SIA)—are advocating for greener manufacturing practices and reduced reliance on hazardous chemicals. Equipment and materials manufacturers are responding by introducing closed-loop systems and more environmentally friendly solvents, but widespread implementation remains costly and technologically demanding.
- Future Prospects: Looking ahead to the next few years, the role of wet plate photolithography is expected to gradually diminish in leading-edge logic and memory manufacturing, while remaining vital for MEMS, sensors, compound semiconductors, and power devices. Ongoing collaborations between tool suppliers and semiconductor manufacturers aim to extend the capabilities of wet processing through improved resist materials, advanced process control, and automation (TOKYO OHKA KOGYO CO., LTD.). However, the sector must continuously adapt to evolving technical and regulatory landscapes to sustain its relevance.
Future Roadmap: Next-Gen Opportunities and Strategic Recommendations
As the semiconductor industry enters 2025, wet plate photolithography remains a foundational process for device fabrication, particularly for mature and specialty nodes where cost and process flexibility are paramount. The technique continues to serve critical roles in MEMS, power electronics, sensors, and display manufacturing, even as leading-edge nodes transition to extreme ultraviolet (EUV) and advanced dry processes.
Several key trends and opportunities define the future roadmap for wet plate photolithography:
- Process Optimization and Hybrid Integration: Ongoing innovation focuses on integrating wet photolithography with other patterning techniques, such as dry and nanoimprint lithography, to enable hybrid process flows. Companies like Tokyo Ohka Kogyo Co., Ltd. are actively developing advanced resists and process chemicals that enhance compatibility and resolution for both wet and hybrid applications.
- Equipment Modernization and Automation: The next few years will see increasing adoption of smart track systems and advanced coater/developer tools, enhancing throughput and uniformity. SCREEN Semiconductor Solutions is expanding its portfolio of automated wet processing equipment tailored for advanced packaging and specialty device manufacturing, supporting higher yields and lower defectivity.
- Sustainability and Environmental Compliance: With tightening global regulations, focus is intensifying on reducing water and chemical usage. Lam Research Corporation and others are investing in sustainable wet processing solutions, including closed-loop recycling systems and low-consumption chemistries. This approach is expected to become a key differentiator for fabs aiming for green manufacturing certifications by 2027.
- Advanced Substrate Compatibility: Emerging applications in compound semiconductors (SiC, GaN) and large-area panels require wet lithography processes adapted for new materials and sizes. SÜSS MicroTec SE is developing photolithography tools capable of handling non-silicon wafers and panel-level substrates, supporting the expansion of advanced power and optoelectronic devices.
- Digitalization and Data Analytics: New track systems are being equipped with AI-driven defect inspection and process control. Tokyo Ohka Kogyo Co., Ltd. and SCREEN Semiconductor Solutions are incorporating data analytics platforms to enable predictive maintenance and real-time process optimization, reducing downtime and enhancing fab efficiency.
In summary, the strategic roadmap for wet plate photolithography in 2025 and beyond centers on process innovation, sustainability, and digital transformation. These advancements will ensure its continued relevance in specialty and legacy markets, while enabling new opportunities in heterogeneous integration and advanced substrate technologies.
Comments (0)